Вы когда-нибудь задумывались над тем, какие испытания проходит холодильник или стиральная машина, прежде чем попасть на прилавок магазина? А в каких условиях тестируют многотонные БЕЛАЗы? Знаете ли вы, на каких стендах испытывают новейшие электробусы, тракторы, комбайны или автобусы и кто стоит за поиском брака в этих высокотехнологичных машинах? Ответы на эти вопросы крайне важны. В Год качества журналисты БЕЛТА заглянули на профессиональную кухню к специалистам отдела качества ведущих производств страны. И своими глазами увидели, как проверяют, оттачивают и доводят до совершенства нашу экспортно ориентированную продукцию. В новом проекте «Испытательный полигон» вы увидите то, о чем раньше вряд ли слышали.
И первым мы расскажем о минском заводе «Атлант». Казалось бы, что может быть проще — положить продукты в холодильник или загрузить белье в стиралку. Когда мы попали на «Атлант» и увидели все этапы контроля, которые проходит бытовая техника с момента начала сборки до отгрузки, то ощущение простоты сменилось изумлением. Это просто космос, Байконур! Малейшее отклонение от параметров — и холодильник, как ракета на старте, не покинет пределы цеха. До тех пор, пока все не будет безупречно. Какая тайна скрыта за пятью печатями ОТК? Что такое персональный штрихкод работника? И как внедряется в многотысячном коллективе философия качества 4.0? Многие ответы вас попросту удивят.
От капучино — до Посейдона
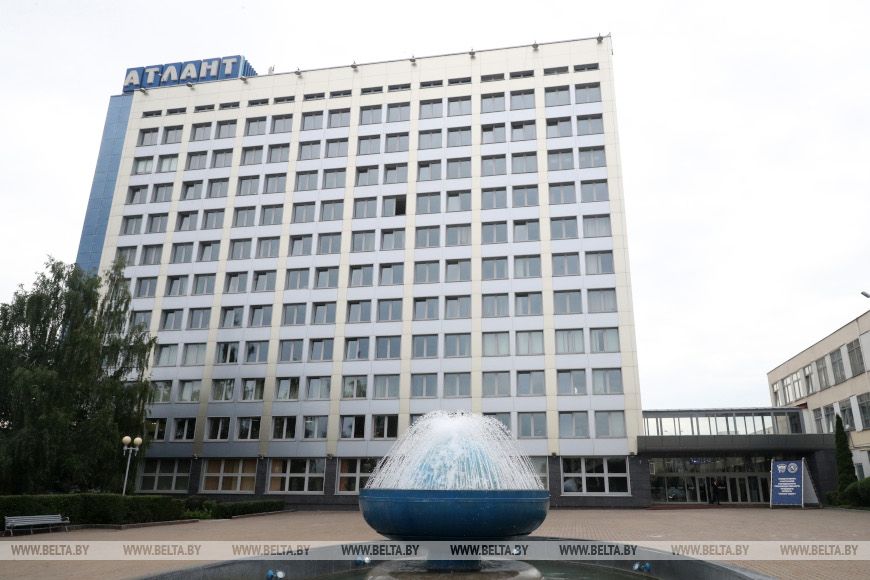
Проспект Победителей, 61 — завод холодильников «Атлант». Каждые сутки из этих стен потребителям из России, Беларуси и других стран СНГ отгружают более 2400 готовых изделий (в сезон — вдвое больше). Заместитель генерального директора ЗАО «Атлант» по управлению качеством Руслан Барановский встречает нас на проходной и сразу интригует: «Современный холодильник — это 1300 деталей и порядка 200 заложенных в него стандартов, которые нужно соблюсти на всех этапах».
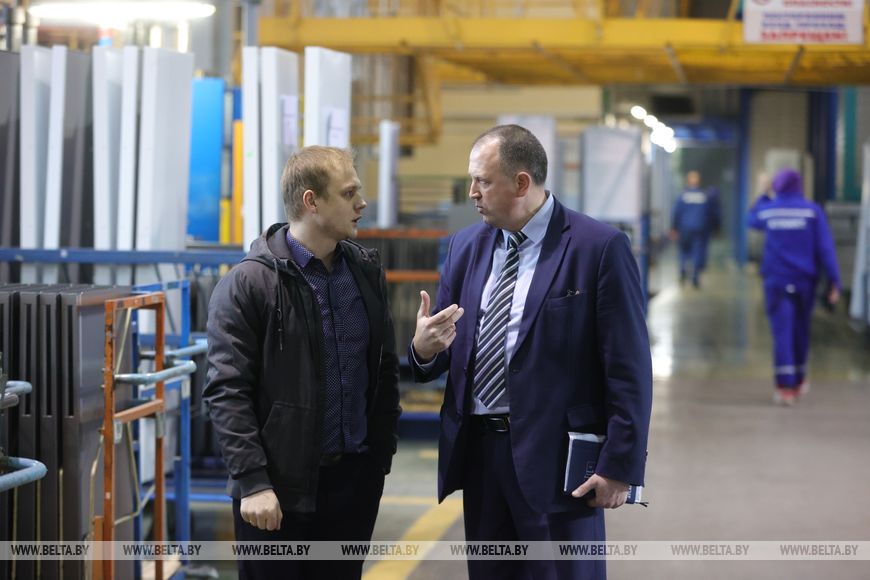
Руслан Барановский пришел на «Атлант» мастером в 2000 году. Видно, что все здесь ему известно до мелочей. И вопрос престижа марки, ее качества — дело всей его жизни. Даже говорит о структуре производства замгендиректора образно, с любовью: «Завод холодильников — это три гигантских кита. Первый — цех обработки металлов. Второй кит — цех пластмасс. И третий — сборочный. На каждом этапе предусмотрен многоступенчатый контроль за качеством, отвечают за который специалисты отдела метрологии и технического контроля бытовой техники (ОМиТК БТ). Сейчас все сами увидите».
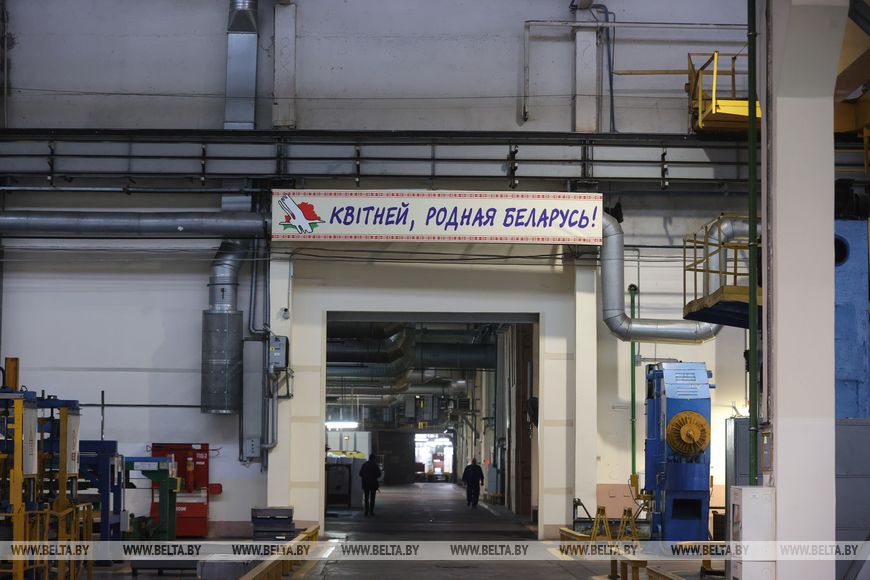
Цех обработки металла — здесь начинает формироваться лицо холодильника. Однотипные листы металла превращаются в рельефные заготовки боковых панелей и дверей. Вдумайтесь: в день цех выпускает 7000-8000 крупногабаритных деталей. И ни на одной из них не должно быть вмятинки, царапинки или отклонения от размера больше чем 0,5 мм. Два контролера несут персональную ответственность, поэтому смотрят зорко и действуют решительно: вмятина — и дверь холодильника уезжает на рихтовку, брак металла — и поставщик получит партию назад. И так две смены, 16 часов в сутки.
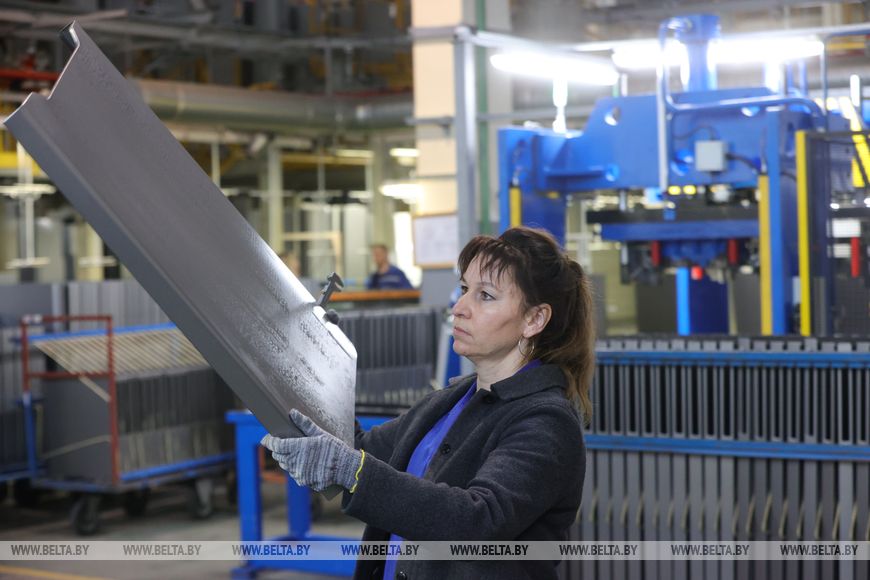
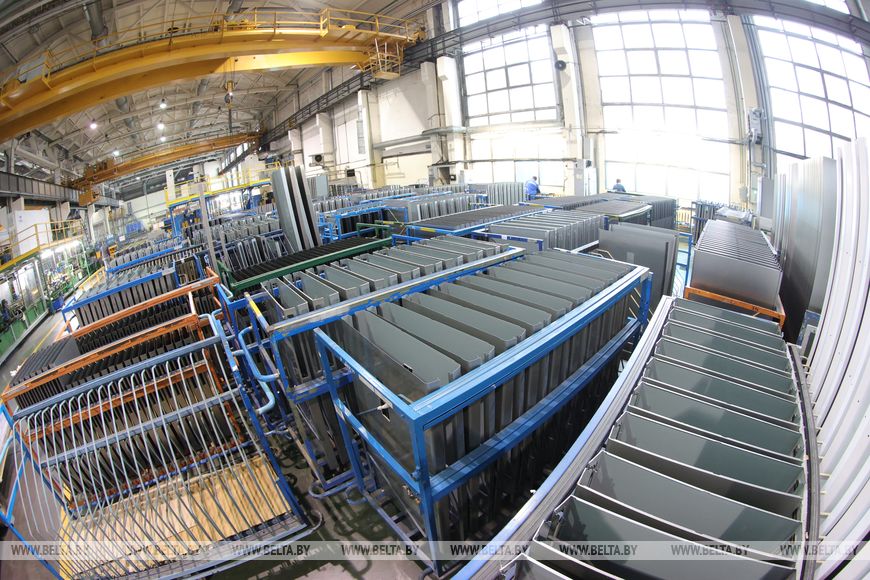
— Мы на участке покраски. Здесь холодильник обретает свой цвет. Палитра широчайшая: от капучино, звездной пыли и салатового до бордового, мокрого асфальта и глубинно черного Посейдона, — легко заглушает голосом работающую немецкую линию Руслан Барановский. — Все эти оттенки маляр знает, как Отче наш. И если краска вдруг неровно легла, цвет вышел ненасыщенный или получилось цветовое пятно, на деталь вешается ярлык брака. Она снимается с линии и отправляется на перекраску. Но это редкость.
Штрихкод, меняющий сознание
Цех пластмасс — второй кит производства. Здесь делают внутренние шкафы — ту самую белую пластиковую внутрянку, которую мы с вами видим каждый раз, открывая холодильник или морозильник. Процесс изготовления — захватывающий! Лист пластиковой заготовки толщиной 4 мм заезжает на линию и тут же попадает в зону шокового разогрева до 600 градусов. Затем под вакуумом ей придают форму нужного шкафа и охлаждают. Все. Заготовка поступает на лазерную обрезку: за несколько секунд луч филигранно выжигает все технологические отверстия.
— Вот, посмотрите, на каждом шкафу — наклейка со штрихкодом. Это означает, что работник на линии тщательно сверил все параметры изделия и поставил свое личное «клеймо». По нему сразу читаю «дата выпуска, модель, табельный номер и ФИО работника», — объясняет контролер Галина Климович. — Я выборочно проверяю шкафы из разных партий, которые идут в течение дня. И если нахожу брак, сразу вижу, кто его пропустил.
— Система персонифицированного учета на «Атланте» начала внедряться в 2007 году. На данный момент оцифрованы 97% всех технологических процессов завода, — рассказывает Руслан Барановский. — Результат? 17 лет назад мы начинали с 20% брака на отдельных участках цеха пластмасс в месяц, сегодня норматив выбраковки по подразделению менее 1%. Технология в корне изменила сознание.
А мы подошли к третьему киту — цеху сборки. Здесь происходит главное таинство: металлический каркас «женят» с пластиковым шкафом.
— Чтобы линия работала бесперебойно, на ней должны трудиться 25 человек. Каждые 46 секунд здесь происходит подсборка холодильника. Представляете, какое это напряжение для сборщиков?! — слесарь-сборщик Виталия Фесун даже не поворачивает головы в мою сторону, а продолжает профессионально сканировать глазами очередной залитый теплоизоляцией полуфабрикат холодильника. На ее рабочем месте на высоте 2 м установлено подвижное зеркало, которое позволяет видеть изделие сверху, сбоку и сзади. Один из шкафов при нас снят с линии. На него клеят продолговатую черную полоску со штрихкодом неисправности — «черную метку». Расшифровываем: модель No Frost, вмятина на панели и продавленная направляющая. После ремонта он снова вернется на линию, и Виталия еще раз досконально его проверит.
Ребус для искусственного интеллекта
— Конвейер — очень тяжелый монотонный труд без права на ошибку. Но человеческий фактор — это неизвестная, которую невозможно спрогнозировать. В начале недели — классический синдром понедельника, раскачка после выходных. Среда — пик недельной усталости. А еще личные моменты: кредит не дали в банке, ребенок двойку принес из школы, с женой поругался… Работник и не хочет пропустить брак, но во власти эмоций и мыслей невольно делает это. Именно поэтому мы сейчас тестируем на заводе систему «технического зрения» с элементами искусственного интеллекта, — раскрывает некоторые секреты Руслан Барановский. — Начнем применять ее в цехе сборки, затем она появится во всех трех цехах-китах. Суть системы в следующем: она просто не позволит работнику и контролеру пропустить брак. Программный комплекс отсканирует изделие, звуком предупредит о проблеме и покажет на мониторе, где есть огрех. Уже летом система будет работать на «Атланте».
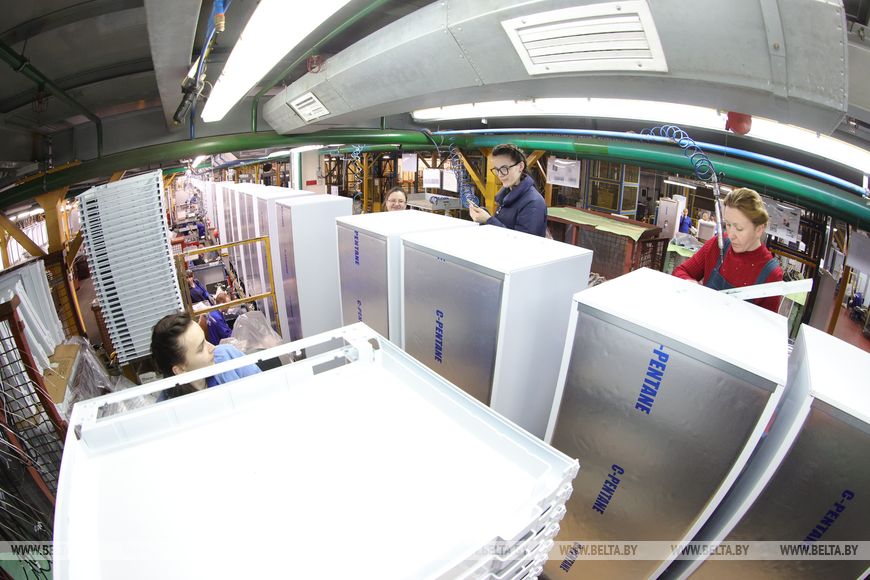
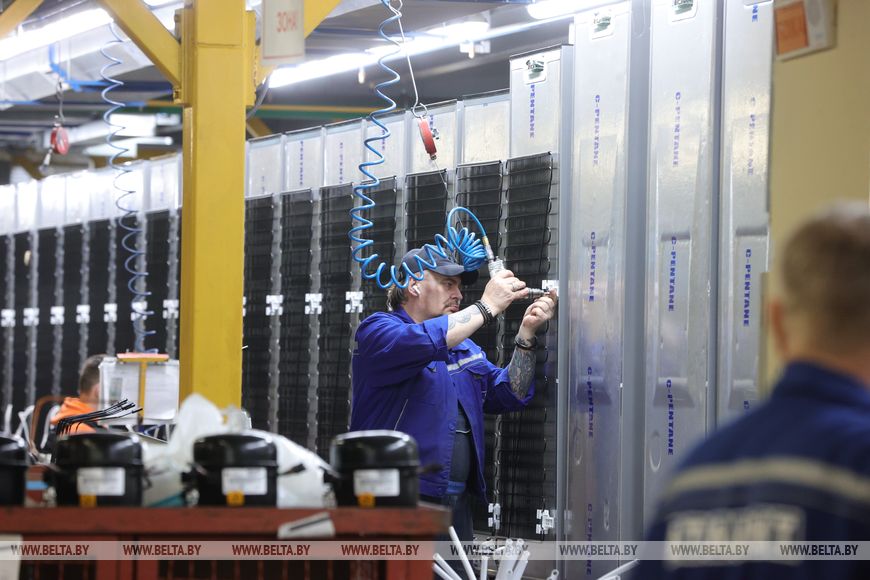
…А мы на сборочном конвейере №1. Сердце и кровеносную систему холодильника — компрессор, конденсатор и патрубки — крепят в строгом соответствии со штрихкодом модели. Пайку выполняют специалисты самой высокой квалификации: у каждого из них есть своя личная синяя печать. Даже если за их спиной раздастся взрыв или завоет сирена, никто не оторвется от процесса. Все слишком ответственно.
— После заправки в систему охладителя происходит спайка и заглушка контура холодильника. И вот тут начинается зона 100-процентного контроля, как на Байконуре при проверке ракеты. Каждый этап досконально проверяет специалист по качеству и ставит личное синее «клеймо». Проверка на короткое замыкание с подачей напряжения до 1000 В — печать! Проверка на герметичность контура — печать! — Руслан Барановский ведет меня по линии контроля (а это отдельные помещения со стальными дверями), стараясь не отвлекать специалистов. — Если на этом этапе всплывает какой-то дефект, устранять его будут только сотрудники ОМиТК БТ.
Холодильники, карусель и красная печать
И вот мы на вершине производственной пирамиды — на испытательной станции завода «Атлант». Это огромная линия карусельного типа, куда, как на Олимп, поднимают готовые холодильники. Их подключают к специальной программе с целым набором параметров и всевидящей термографической камерой. Если коротко, холодильник заставляют попотеть, прогоняя на максимальных режимах. Цель — найти температурные отклонения или утечки.
— Вчера выявили неработающий температурный датчик в морозильной камере. Вскрыли холодильник — теперь ищем причину неисправности. Когда найдем, все поправим и снова запустим на линию, — ведет меня через железный движущийся поток готовой продукции Дмитрий Залукаев — начальник участка испытаний и ремонтов ЗАО «Атлант». — В целом выбраковка по итогам приемо-сдаточных испытаний за месяц у нас не превышает 1,5%.
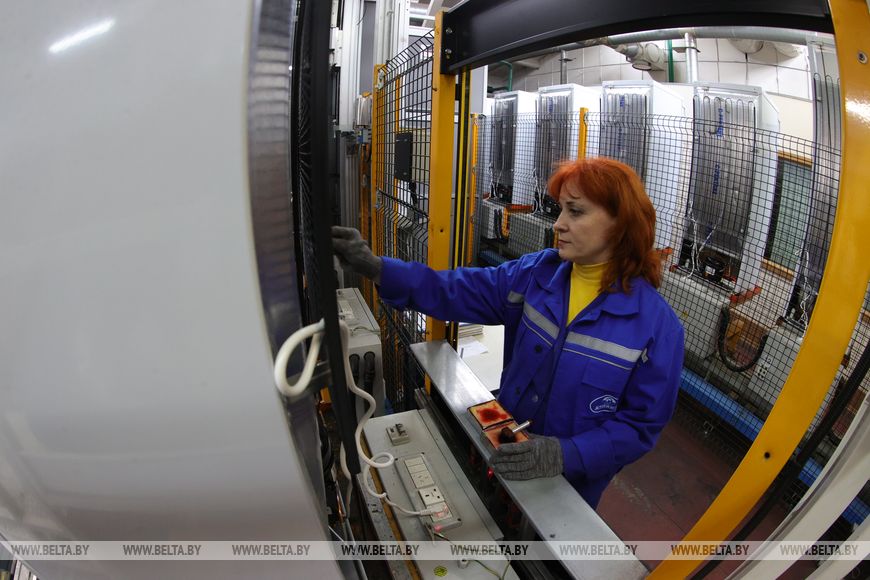
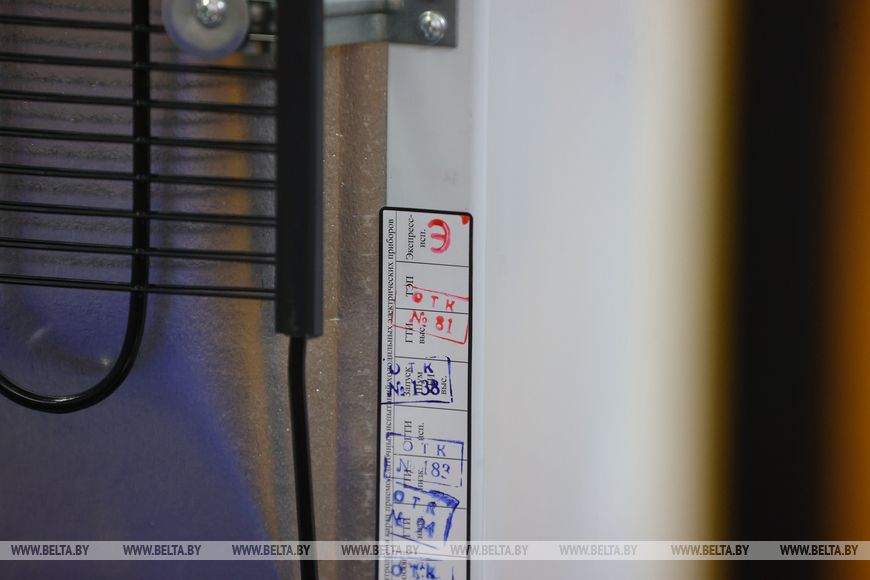
Тем временем контролер Наталья Денисик фиксирует показания с очередного завершившего цикл проверки холодильника на линии. «Брак не выявлен!» — красноречиво сообщает компьютер в чеке-распечатке. Наталья берет со стола красную печать ОМиТК БТ и смачно ставит ее поверх 5 синих. Вот и все, 6-часовой этап производства, сборки и контроля позади!
— Указ Президента по Году качества подтолкнул нас к переосмыслению своих прежних наработок и поиску новых. К концу года планируем показатель брака на приемо-сдаточных испытаниях снизить до 0,7%. В том числе за счет внедрения технологии с элементами искусственного интеллекта, — рассуждает Руслан Барановский, пока мы переходим на линию упаковки. — Представьте, в месяц «Атлант» выпускает десятки тысяч холодильников и морозильников — огромная цифра! Если по итогам года по показателю эксплуатации мы добьемся меньше одного процента брака, это будет большой шаг вперед. Это миллионы рублей, сэкономленных для предприятия.
«Первые годы работы они мне снились»
…Из 30 экспертов, которые работают на линии упаковки, есть 2 с приставкой «супер». Одна из них — контролер ОМиТК БТ Алла Пристром. Она работает на «Атланте» уже почти 25 лет и с расстояния в 30 м определит модель и комплектность любого холодильника:
— Здесь, на упаковке, мы по сути проводим еще один 100-процентный осмотр холодильника. Проверяем на вмятины, сколы, комплектность, устраняем мелкие зазоры и перекосы, даже на токсичные запахи проверяем. Еще раз моем. Помню, в первые годы работы холодильники мне снились каждую ночь: я очень боялась, что пропущу какой-то дефект… Теперь уже не снятся. Но когда прихожу в торговый центр за покупками, обязательно подхожу к холодильникам других брендов, бегло осматриваю — и всегда вижу, где недоработал контролер, — смеется Алла Пристром. — Могу с уверенностью сказать: после меня в упаковке с надписью «Атлант» возвышается очень красивый и качественный продукт. Его собрали сотни рук и тщательно проверили сотни глаз.
…Но даже несмотря на весомый аргумент с фамилией Пристром, со склада готовой продукции специалисты по качеству выбирают еще около 2% готовых к отгрузке холодильников. Вот этот, этот и воо-он тот! Распаковывают, достают, тестируют на разных режимах, сверяют комплектность и качество сборки. Только после этого партию отгружают в розничную сеть.

— Кому-то такой многоуровневый контроль может показаться излишним. Возможно. Но наше предприятие экспортно ориентированное, 60-70% продукции уходит за пределы страны. Поэтому все эти годы «Атлант» делает ставку на полный заявленный срок службы своих изделий: они должны отработать минимум 10 лет, — раскрывает производственные секреты Руслан Барановский.
Что такое «тест ОК» и «чек брака»
С завода холодильников мы берем курс на Шабаны. Здесь находится второй завод «Атланта», с 2007 года выпускающий известные всему СНГ стиральные машины. Каждые 27 секунд с конвейера сходит новенькая сияющая стиралка-автомат.
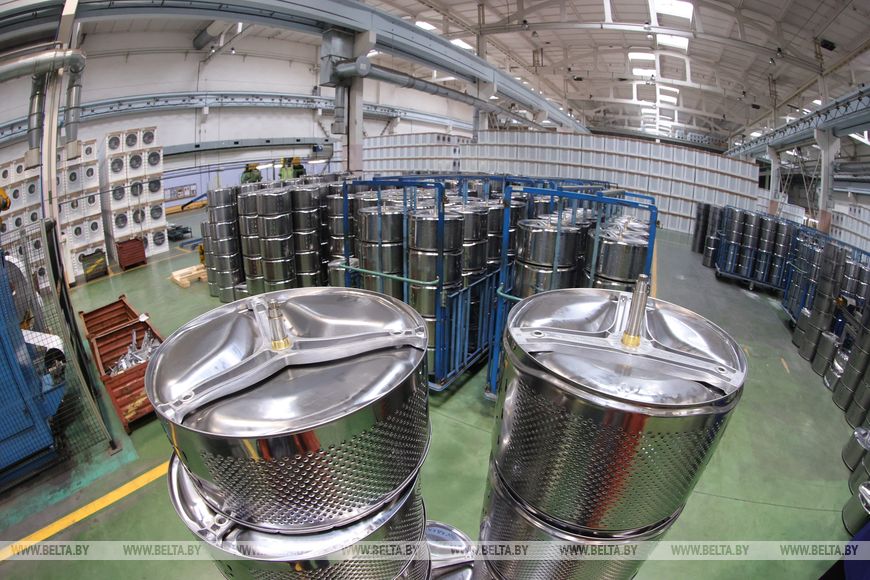
— У стиральной машины, конечно, не 1300 деталей, как в холодильнике «Атлант», а вдвое меньше. Но цикл производства очень похож, — начальник производства Александр Орловский поэтапно знакомит нас с внутренней кухней предприятия. — Вот здесь, на первой линии, изготавливают барабан, на второй — корпус, на третьей — красят, на четвертой — «женят» двигатель с каркасом. На пятой — полностью собирают стиральный агрегат. При этом важнейшие моменты узловой сборки зорко бдит компьютер. Чуть не дожал винт или амортизатор — и тут же получишь «нагоняй» от электроники.
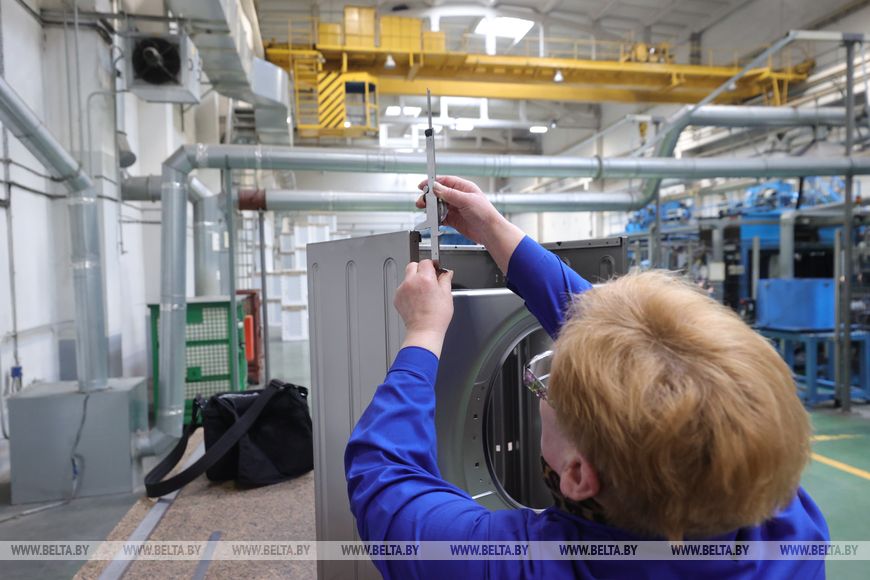
Оставим за кадром подключение и монтаж узлов. Все самое интересное начинается на станции приемо-сдаточных испытаний.
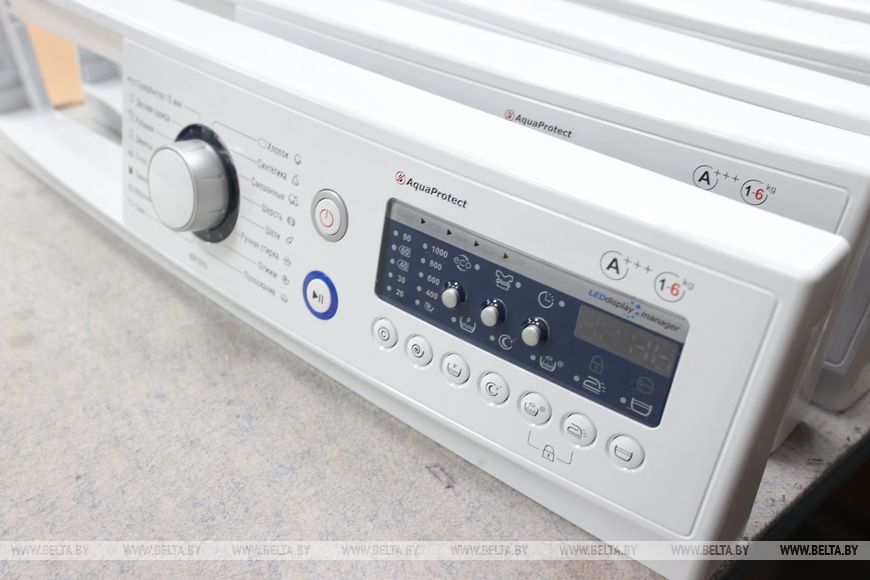
— Каждую стиральную машину подсоединяют к специальному программному комплексу, который испытывает ее по полной. Утечка тока, проверка оборотов двигателя, налив воды, работа всех функциональных клавиш модуля управления — на это уходит не менее 5 минут. По завершении, если все системы работают корректно, комплекс выдает чек: «Тест ОК», — ведет меня через белоснежные ряды подключенных машин Ольга Дрозд — заместитель начальника ОМиТК БТ ЗАО «Атлант». — Ну, а если нет — на бумажном корешке выйдет код ошибки. Как мы говорим, чек брака. Машину снимают с линии и отправляют на участок ремонта: здесь неисправный модуль меняют либо чинят. И она снова становится на линию приемо-сдаточных испытаний.
После того, как получен «Тест ОК», партия… не отправляется на упаковку. Два процента от выпущенных в смену машин отвозят на станцию выборочных функциональных испытаний. Это означает 3 часа 57 минут стирки в режиме «Хлопок, 60 градусов». В 99,9% случаев все проходит идеально. Но работники завода еще помнят случай, когда несколько лет назад после обнаружения двух одинаковых дефектов в отобранных стиралках пришлось отозвать всю партию. Бывает и такое.
Победители марафона выносливости
Руководитель группы ресурсных испытаний ЦИЭР БТ Игорь Замыслов скромно говорит, что знает о стиральных машинах больше любой многодетной мамы. Он работает на заводе с 2009-го и восемь часов в день тестирует режимы стирки на машинах различных интерфейсов. Вдоль стен лаборатории стоят в ряд несколько десятков стиралок — они усиленно крутят барабаны с бельем…
— Сегодня, например, у нас на проверке десятый интерфейс. Из выпущенной за смену партии я точечно отбираю 20 машин на выборочный контроль. Осматриваю узлы двигателя, тэнов, клапанов, амортизатора. Снимаю крышку и заднюю стенку, подключаю агрегат по сертифицированной методике к испытательному стенду — и наблюдаю на компьютере в режиме онлайн все показатели его работы. Час они стирают в режиме «Хлопок-90» без белья, затем еще 3 часа в том же режиме с бельем. Если замечаний нет, стиральную машину моют, сушат, упаковывают и отгружают потребителю. В случае брака собираемся комиссионно с конструкторами, специалистами по качеству и ставим диагноз. Единичную неисправность быстро устранят. Если дело серьезнее, притормозить придется всю партию.
Особняком у дальней стены лаборатории надрываются 5-7 стиральных машин различных модификаций. Они не имеют никакого отношения к партии, выпущенной заводом сегодня. Их задача, как выяснилось, просто стирать: днями, неделями, месяцами и даже годами.
«Например, решил главный конструктор протестировать новый блок управления. Этот узел монтируется в указанные машины, и их запускают в 8-часовом режиме эксплуатации. По сути, это марафон на выносливость и надежность нашей техники, — говорит Игорь Замыслов. — Вот эта машина, возле которой вы стоите, работает уже почти 12 лет. Остальные меньше: вот эта 5 лет, эта 7, эта 4 месяца. Вообще же, по нормативу любая наша машина должна гарантированно выполнить 1850 стирок. По сути, это 10 лет эксплуатации».
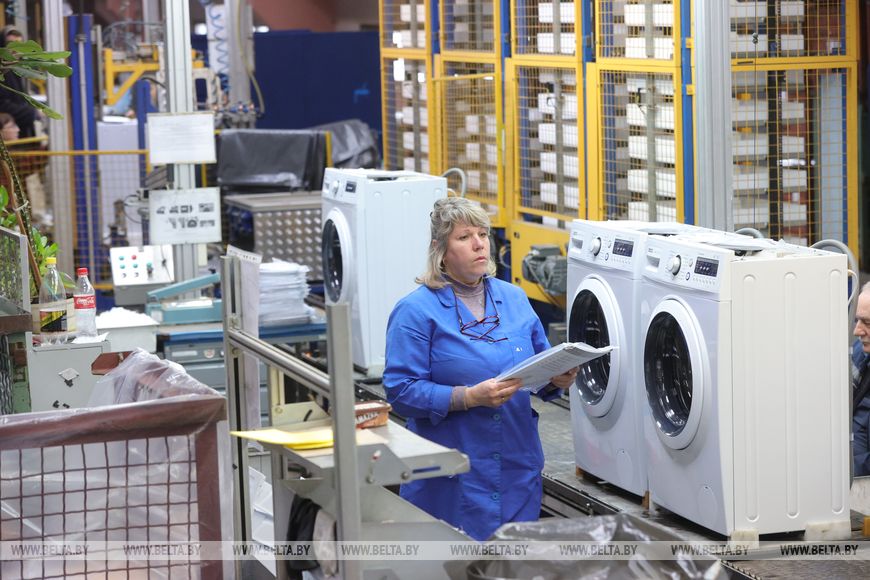
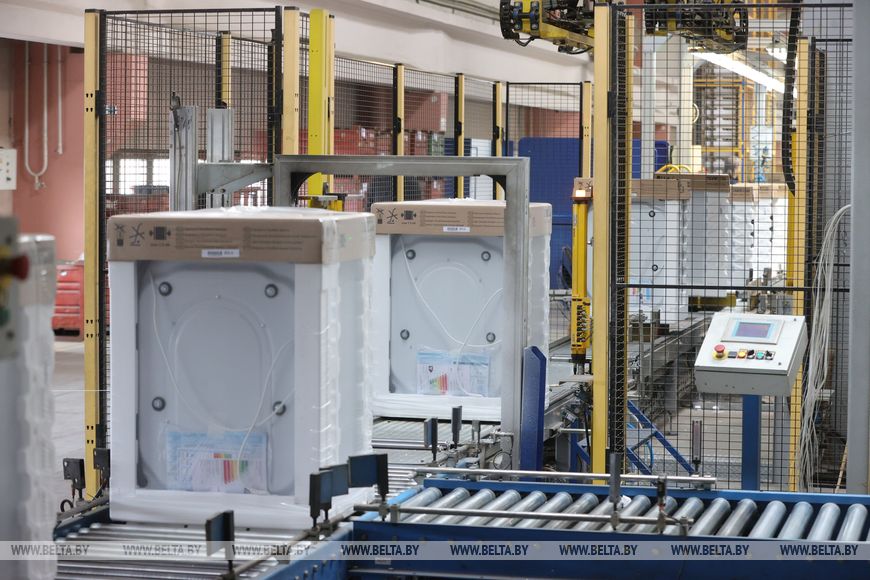
— Я убежден, что Год качества всем производствам страны нужно рассматривать не просто как технологический вызов и ряд новых задач для службы ОТК, — Руслан Барановский провожает нас со склада готовой продукции к машине. — Нужно посмотреть на производственный процесс с нового ракурса — с точки зрения переформатирования сознания работников, постижения новой философии KPI. Да, технологические новации позволят нам повысить планку контроля за качеством и снизить уровень дефектности. Но нужно поэтапно, год за годом добиваться и другого — привить каждому работнику предприятия внутреннее чувство нетерпимости к браку. Заразить этой идеей весь коллектив! И в идеале добиться того, чтобы у нас работали люди, в принципе не нуждающиеся в контроле. Скажем, на 150 работающих — один контролер и какой-то летучий, выборочный по сути, аудит. Все. Во главу новой философии качества 4.0 нужно положить совестливость, осознание своей важности в производственном цикле и ответственность за конечный результат. Тогда и холодильник, и стиральная машина получатся другими. Поверьте мне на слово, это будет бытовой шедевр! Ведь коллективная положительная энергия никуда не исчезает — она передается технике и магнитом тянет к себе покупателя.